6 Steps to Implementing Automation
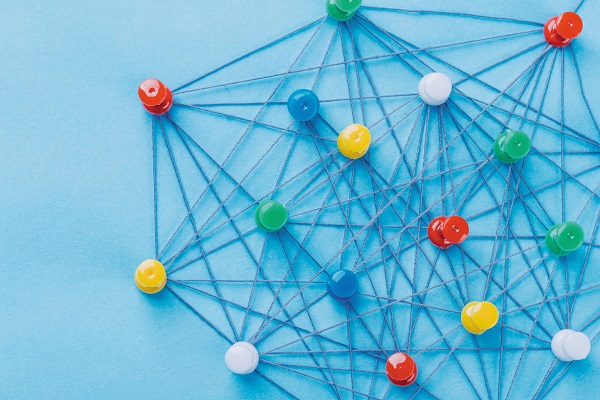
By: Martina Seferovic
Demand for business automation has increased over the last two years, according to a 2022 survey by Salesforce and Vanson Bourne. Meanwhile, the robotic process automation (RPA) software market grew 19.5% in 2022 compared to 2021 and was anticipated to finish 2023 with 17.5% growth, according to an August 2023 analysis from Gartner. By 2025, 70% of organizations will implement full automation in infrastructure and operations, an increase from 20% in 2021.
In the coming years, the combination of artificial intelligence (AI) and RPA is set to play a pivotal role in transforming the insurance industry. As these technologies continue to advance and gain broader acceptance, companies that strategically embrace and implement them are likely to gain a competitive advantage in the market.
However, the road to automation is paved with challenges and complexities that require careful planning and analysis. While the promise of increased efficiency and streamlined process beckons, successful implementation hinges on a number of factors.
A critical step in the transformative journey to automation is business process optimization—but it is often underestimated. Why? Many organizations are eager to embark on digital transformation and fail to prioritize the audit and optimization of business processes. Often, this is due to the allure of quick fixes and immediate gains that automation promises. When faced with pressure to improve efficiency and reduce costs rapidly, organizations jump straight into implementing automation solutions without thoroughly examining their existing workflows. The rush can lead to the automation of inefficient or outdated processes, exacerbating inefficiencies rather than resolving them.
Another reason businesses neglect process optimization is a lack of awareness or understanding of its benefits. Some organizations might view process optimization as a time-consuming and resource-intensive endeavor, not realizing the long-term advantages it offers. In pursuing automation, they may overlook the fact that optimizing existing business processes lays a solid foundation for successful automation initiatives. Without streamlining processes first, automation can become a band-aid solution that fails to address underlying issues.
Furthermore, the complexity of some business processes may deter organizations from attempting to optimize them. They perceive certain workflows as too intricate and challenging to revamp. However, automating complex processes that have not been cleared of deficiencies can lead to automation bottlenecks and fail to deliver the desired results.
Steps to Success
For automation to be successful, it is critical to ensure the process that is going to be automated is streamlined and free of any deficiencies. The chances are that the longer the process has been around, the more inefficiencies it has.
Here are six steps to guide you through the audit process:
Step 1: Review task manuals and SOPs. Begin the audit process by reviewing existing task manuals and standard operating procedures (SOPs). These documents provide valuable insights into how processes are officially structured. However, it is important to recognize that the actual practices might differ from what is documented, as employees may make ad hoc modifications to processes over time. Being aware of potential discrepancies sets the stage for in-depth observations and understanding.
Step 2: Observe processes in action. Merely relying on documentation is insufficient to gain a holistic view of business processes. Physically engaging with the teams and observing how processes are executed in real-time provides a broader picture. This on-the-ground approach illuminates the process’s nuances, identifies bottlenecks and highlights the challenges faced by employees. It also provides an opportunity to gather direct feedback from those performing the tasks, ensuring a comprehensive understanding of the process.
Step 3: Document the current state. Create a detailed record that documents the existing process as it is practiced and the ideal state the organization aims to achieve. This comparative analysis sheds light on gaps between the current and desired states, providing a roadmap for improvement. Ask a series of questions during this documentation phase: What steps are necessary? What steps can be removed or streamlined? Is there a more efficient way to achieve the desired outcomes?
Step 4: Benchmark against best practices. Incorporate insights from similar companies and industry best practices into the audit process. Studying and analyzing how successful organizations handle similar processes can offer valuable benchmarks for optimization. Comparing your current processes with industry-leading practices helps identify areas that require attention and enables you to adopt tried and tested methods.
Step 5: Question and analyze every step. During the audit, encourage a culture of inquiry where every step of the process is questioned and analyzed. Challenge the “we have always done it this way” narrative and identify areas where processes might be unnecessarily complex or outdated. Emphasize the need to innovate and embrace change, even if certain practices have been in place for years. This type of evaluation ensures that only the most efficient steps are retained in the optimized process.
Step 6: Involve a diverse review team. To gain comprehensive insights and perspectives, involve a diverse team of individuals from different departments. Engage those who are closely associated with the process on a daily basis, as well as others who may offer a fresh perspective. A mix of technical and non-technical staff ensures a well-rounded examination of the processes, resulting in better decisions.
Prioritizing Processes to Optimize and Automate
Decision-makers don’t always have firsthand experience with the day-to-day processes within their organization. This can result in misconceptions regarding which processes are most suitable for automation. For example, it is natural to be tempted to automate numerous processes at once or those that have been around the longest. However, they are usually not the best measures of automation suitability.
Before delving into the resource-demanding and costly journey of task optimization and automation, consider the following:
Is the task repetitive and involving minimal human input? When identifying processes for automation, start with tasks that are highly repetitive and involve minimal human intervention. These tasks are usually the most suitable for automation because they often follow set patterns and are prone to human error.
Is the task frequently performed? Focus on automating high-volume processes that have a significant impact on daily operations. By automating frequently performed tasks, organizations can realize substantial efficiency gains and rapid returns on their automation investments.
Is the projected benefit of automation worth the investment? Before deciding to automate a task, perform a cost-benefit analysis. Will the anticipated benefits of automation justify the investment? Calculate the potential time and cost savings, improved accuracy and increased productivity that automation can bring to the process.
Martina Seferovic is CEO of OIP, an American-owned knowledge process outsourcing (KPO) company headquartered in Henderson, Nevada. OIP has processing centers in Serbia, Croatia and India.